2D and 3D Rebar Detailing – Advantages and Disadvantages
What is Rebar Detailing?
Rebar is a common construction material that is used in concrete structures. It is created by winding steel around another object, typically a bar or mesh. The rebar can then be embedded in concrete to provide strength and support for structures. In this article we talk about Advantages and Disadvantages of 2D and 3D Rebar Detailing.
Rebar Detailing is an important part of the construction process. It involves determining how much rebar is needed for each structure, where it should be placed, and what size it should be. This information can then be used by construction workers to place the bars properly and ensure that they reinforce the concrete as it hardens.
Rebar Detailing is a procedure of making shop drawings of the steel reinforcement for fabrication and development. The Rebar Detailing procedure involves the positioning, bending shapes, amount, description, laps of the reinforcing steel, and measurements. The Reinforcement Drawings are made to incorporate various specifications such as the separation, area, rebar size and lap of steel. Rebar detailing is a complex and time-consuming process that involves turning a vague structural plan into a precise positioning drawing and bar bending schedule. It improves the quality of the structure and lowers project cost overruns.
The structural drawing and the reinforcement instructions received from the structural engineer are read in depth by the Rebar Detailer till he understands the structure. He also should know the fabricators’ practices and contractors’ construction schedules and requirements. The Detailer should also do spacing calculations and calculate the quantity of the Rebar and list the Rebar dimension, providing a bar mark for grouping and fabrication requirements. He also needs to prepare a placing drawing to give visual placing instructions for the Rebar placers on the site.
Advantages of 2D Rebar Detailing
- Rebar Detailing prepares an error-free Bar Bending Schedule, and at the time of fabrication, it should fit in the concrete formwork without any issues. The same Bar Bending Schedule will be used for accounting and invoicing.
- Rebar placing drawing provides guidance in such a way that the Rebar can be placed correctly on the site without any issues.
- Rebar Detailing helps the structural engineer verify and approve if the structural design intent is properly converted into the Reinforcement drawings and Bar Bending Schedules.
- Rebar Detailing can reduce unwanted costs by analyzing rebar wastage and potential scrap existing at the site.
- Rebar Detailing contributes to increasing the overall efficiency of the project. Once prepared, they help to carry out the fabrication and placement of reinforcement quickly and effectively.
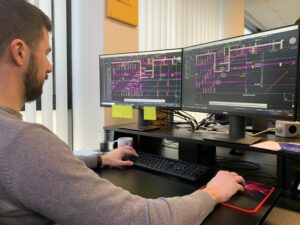
Disadvantages of 2D Rebar Detailing
- Reinforcement drawings are subject to design errors and typos. This led to incorrect fabrication of steel and loss of material. Furthermore, they add additional expenses to the construction.
- Rebar Detailing for massive and complex reinforcement structures demands high accuracy and precision. It is possible that the Detailer may accidentally omit some rebar measurements in the plan. These errors are often noted only after the drawings are issued.

With the advancement of 3D modeling technology, Rebar Detailing may now be developed and modeled in three dimensions. This brand-new, specialized programme for Rebar Detailing aids in the design, documentation, tracking, and management of every structural part. The creation of an effective and accurate reinforcement model is made possible by the ability to import structural calculations from structural analysis applications using the appropriate Rebar Detailing solution. Contrary to manual modifications to 2D views and sections, automation also makes 3D Rebar Detailing changes as well as updates to drawings and schedules rapid and easy.
Advantages of 3D Rebar Detailing
3D rebar detailing has many advantages over 2D drawings. Some of them are given as follows:
- Structural engineers can produce design reports, drawings, and schedules from 3D modeling more rapidly and easily than from 2D design.
- Cost forecasts are accurate because the rebar amounts generated from the 3D model are more trustworthy than take-offs from a 2D drawing. Quantities are completely traceable as well, making checks and comparisons simple.
- Detailing reinforcement in 3D is not only faster, but it essentially eliminates the clashes as you can instantly see the prepared model will not fit into the respective area.
- Reinforcement detailing can be reviewed in digital representation before it is ordered from the contractor, and complex settings can even be assembled off-site.
- 3D drawing greatly reduces the congestion created by the various clashes of reinforcement detail in 2D drawings, and the errors can be spotted and fixed much earlier in 3D drawings than 2Ds.
- The 3D model shows every single bar in the exact position, and it can be fixed as well as any existing obstructions, etc.
- The rebar fabricator can take data directly from the model to its machinery rather than relying on manual input from paper schedules.
- Concrete pours can be defined in the 3D model along with its volumes and quantities, creating more accurate management of material deliveries with greater control. This also minimizes waste and reduces costs.
- The advantages of a comprehensive digital model extend beyond the engineering and detailing stages. When it comes time to fix the reinforcement on site, the contractor can be confident that it will fit because it has been properly modeled in 3D.
- Contractors can use the 3D rebar drawings to create an understanding of the overall structure. They can also frame a model layout and track the quantity of rebar materials needed.
- Instead of depending on deciphering conventional 2D drawings, the fixers can view the rebar in the model environment on the job site, providing them with an immediate and accurate understanding of what is needed.
- By providing features like clash detection and on-site 3D model interrogation, 3D Rebar Detailing significantly improves the overall detailing procedure.

Disadvantages of 3D Rebar Detailing
While 3D Rebar Detailing offers numerous advantages, there are also some disadvantages to consider:
- Initial Learning Curve: Transitioning from traditional 2D Detailing to 3D Rebar Detailing may require additional training and expertise. Structural engineers and Detailers need to familiarize themselves with the software and techniques used for creating and manipulating 3D models.
- Software and Hardware Requirements: Implementing 3D Rebar Detailing often involves investing in specialized software and hardware systems. These tools can be expensive, and regular updates and maintenance may also be required.
- Time and Cost: While 3D Rebar Detailing can save time and improve accuracy in the long run, the initial process of creating the 3D model may require more time compared to traditional 2D drawings. Additionally, the cost of software licenses and training may be an added expense for companies.
- Collaboration Challenges: Collaborating with other stakeholders, such as architects, engineers, and contractors, may pose challenges when working with 3D models. Ensuring compatibility and smooth data exchange between different software platforms can be a complex task.
- Model Complexity: As 3D rebar models become more intricate and detailed, managing the complexity of the model can be challenging. Large and complex models may require powerful hardware to manipulate and visualize effectively.

Summary
To sum up, Rebar Detailing is a crucial process in construction that involves determining the placement and size of rebar in concrete structures. It improves structure quality and reduces project cost overruns. 2D Rebar Detailing offers advantages such as error-free bar bending schedules, proper guidance for placement, cost reduction, and increased project efficiency. However, it can lead to design errors and typos.
With 3D modeling technology, Rebar Detailing can now be done in three dimensions. 3D Rebar Detailing has several advantages over 2D drawings, including faster production of reports and schedules, accurate cost forecasts, clash elimination, and better visualization. It allows for review before ordering, reduces congestion, and enables direct data transfer to fabricators. Concrete pours can be defined accurately, minimizing waste and reducing costs. Contractors can create an understanding of the structure, and fixers can view the rebar on-site for immediate understanding.
However, there are some disadvantages to 3D Rebar Detailing. It requires additional training, specialized software, and hardware systems. Initial model creation may take more time and incur extra costs. Collaboration challenges, model complexity, data integrity, resistance to change, and project size considerations must be addressed. Maintaining and updating the models can be time-consuming, and ensuring accessibility and compatibility among stakeholders is crucial.
The significance of the disadvantages depends on project requirements, available resources, and industry expertise and adoption.
What are your thoughts on this subject?